How do you make construction environmentally friendly? These Scottish companies are finding ways to answer that question.
Construction industries contribute almost 40% of carbon dioxide emissions worldwide. When construction companies also make up over 10% of all Scottish companies, there is a clear need to develop sustainable techniques and materials if Scotland hopes to meet the goal of net zero carbon emissions by 2045. Fortunately, Scotland’s construction industry is proactive in this process and is leading the way for its global partners. Across different sectors of the industry, innovation is creating exciting new opportunities for sustainable construction.
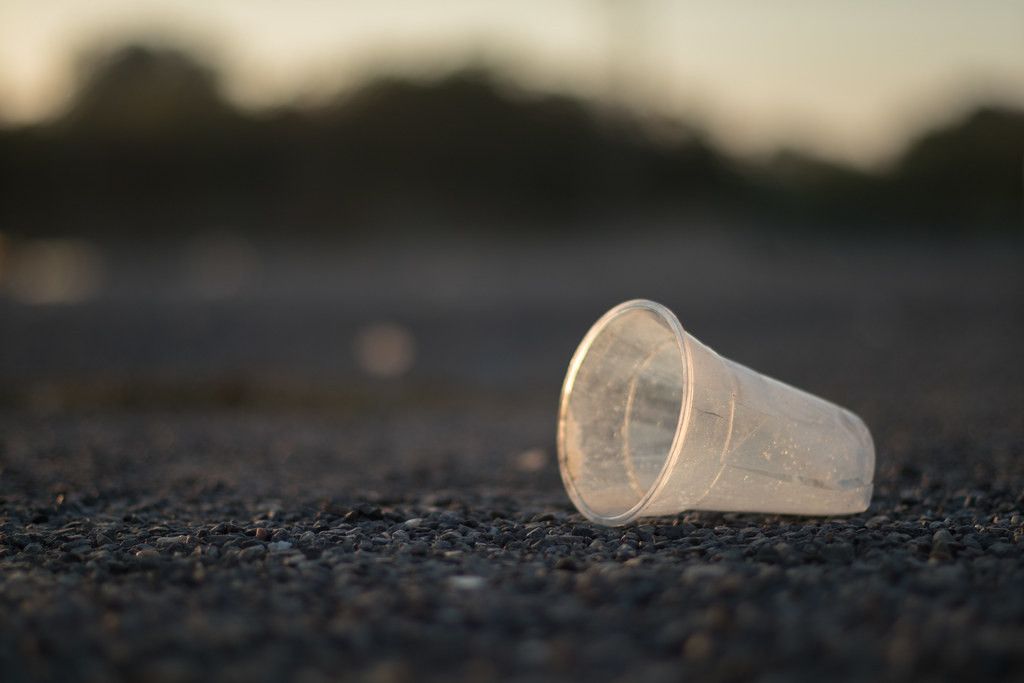
Paving the road to sustainability
One such company is Lockerbie-based MacRebur. Formed by Toby McCartney with his friends Nick and Gordon, the company take plastics destined for landfill and granulate them to make an enhanced asphalt material for roads. The idea originated while Toby was working in Southern India, where he saw plastics from landfill used to fill potholes. Road menders packed the plastic into cracks, poured diesel over the top and set the mix alight until the plastic melted into the crater to seal the pothole.
Since then, MacRebur has shared its products around the world, from Scotland, England and Wales to South Africa, Estonia, Slovakia and even the USA. Their plastic products are used to bind an asphalt mix, meaning the volume of Bitumen (the semi-solid petroleum material used in roads) is reduced. Not only is MacRebur producing a more sustainable alternative to the crude-oil run-off, Bitumen, but their process is also cheaper. Although it only makes up 4-5% of an asphalt mix, Bitumen is the most expensive component of road paving mixtures. A win all-round for the construction industry, and the planet.
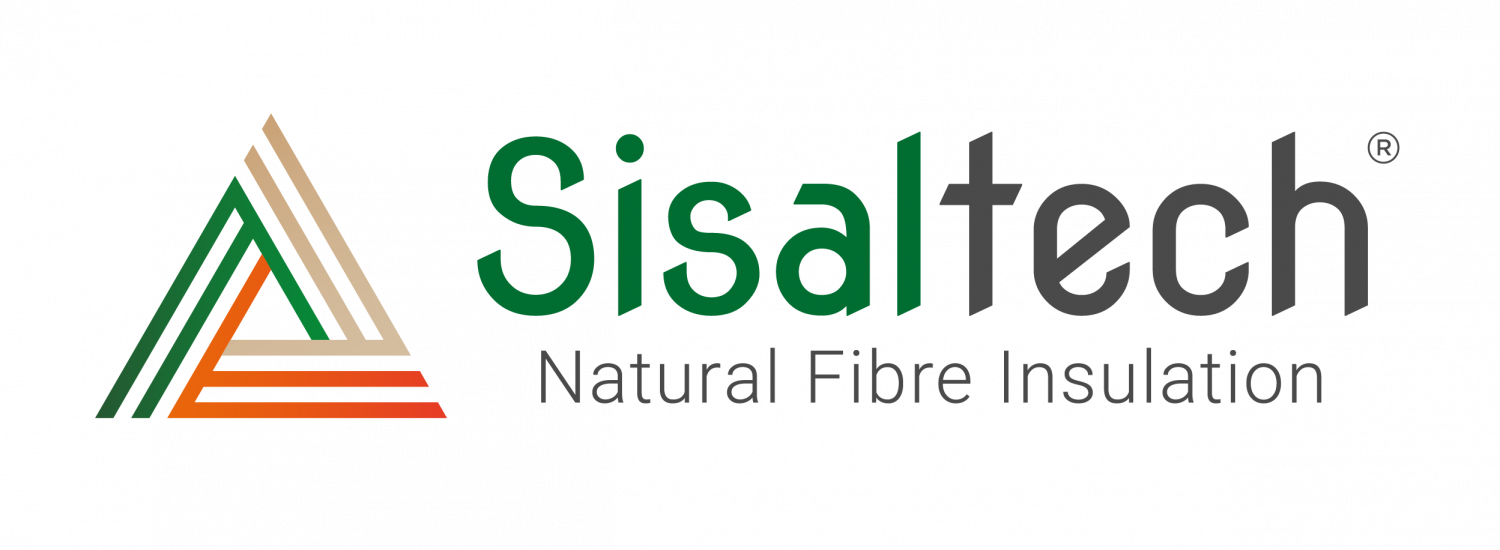
New life for old techniques
You might not have heard of the Sisal plant, which is native to Mexico, however one Scottish firm, Sisaltech, has found a way to use its strong fibres to create sustainable building insulation.
The plant was traditionally used to create rope and other items that needed to be hard-wearing, such as carpets. Sisaltech is working with independent farmers across eastern Africa to produce Sisal, which is both high yielding and consumes minimal water, meaning it is a highly sustainable crop for small-scale farmers to grow.
The firm’s aim is to tackle climate injustice by giving those most impacted by climate change an extra income stream to help them improve their lives, to conduct their business in the lowest carbon way possible, and to manufacture innovative and sustainable products.
Not only is Sisaltech’s product made from sustainable resources, but the insulation can also enable buildings to become more energy efficient, saving both money and reducing their carbon footprint. Because the insulation material has natural moisture ‘buffering’ (meaning it doesn’t absorb condensation or damp within a building) it can be used in historic buildings, keeping them warm in winter, and cool in summer, without the environmental and financial costs of additional heating.
Sisaltech has even thought about the wasted offcuts too; the use a natural, starch-based binding agent ensures that any left-over material from a project is entirely compostable. From start to finish, Sisaltech has got sustainable practices covered.
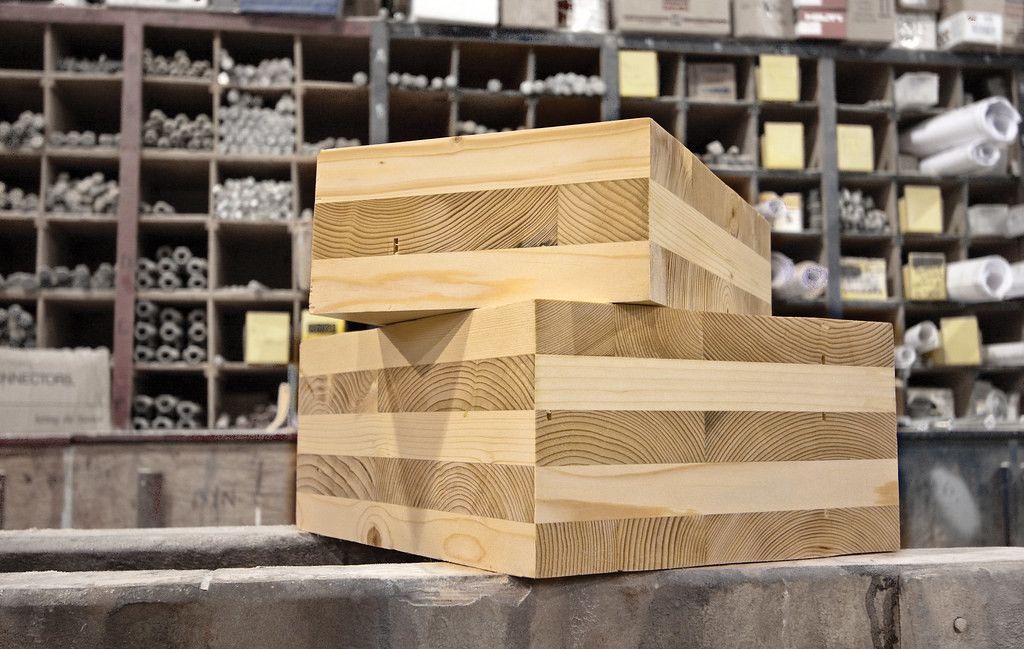
Cutting Carbon in Construction
In the early 1990s, in Germany and Austria, cross-laminated timber (CLT) was developed as a structural construction material in answer to supply shortages of fresh timber. Since then, CLT has grown in popularity for its sustainable properties, and companies such as Scotland’s CCG is putting it to the test in exciting new ways. In 2018 their residential project on Ellerslie Road in Glasgow won a Structural Timber Award for constructing all seven storeys using CLT. By using CLT instead of traditional timber construction, the project removed the equivalent of 757 tonnes of CO2 from the Earth’s atmosphere.
There are several ways in which CLT can reduce CO2 emissions and even remove CO2 from the atmosphere. The first is by harvesting timber from diverse-age forests. This means that as one group of trees is harvested, the volume of timber is replaced by new trees, so there is no net loss of forestry, which in turn means that the trees will continue to absorb CO2. The second is in storage. CLT construction ensures that the CO2 the tree captured during its life is not released into the atmosphere (as it would be if the timber was used for fuel), so the wood acts as a long-term natural carbon storage system. Finally, CLT production is much less carbon-intensive than manufacturing alternative construction materials such as steel or concrete.